— By Walter Fluharty —
Roofing is risky business — safety is everyone’s business.
While we know safety is always important throughout the year, June celebrates National Safety Month to bring increased awareness on how to prevent injury and death anyplace, including the workplace. Roofing is the fourth most dangerous job in the United States, according to the Bureau of Labor Statistics. The most common causes of injuries and deaths are fall-related incidents, which are also the most cited OSHA violations.
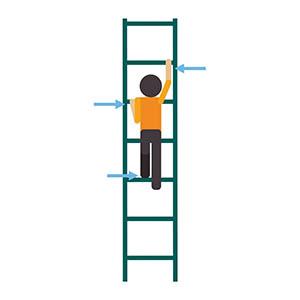
Rooftop safety is serious business, but roofing companies aren’t the only responsible party — building owners and managers share in the responsibility for providing safe roof access for both employees and vendors.
In addition to roofers, there are many others who need rooftop access including facility management staff, HVAC contractors and utility workers. For restaurants, there is also traffic from contractors installing and cleaning the grease gutters or grease containment systems. Any type of incident with them — or anyone on the roof — could result in negative publicity, downtime and disruption to a business or worst of all, injuries or fatalities. In addition to the serious human aspect of these, incidents can also result in related investigations, liabilities and OSHA citations/penalties.
Establishing a Rooftop Safety Program
The best way for building owners and managers to avoid roof-related risks is to establish a documented rooftop safety program for every building. It’s a document that should be updated regularly and reviewed by every person before accessing the roof.
Here are a few essential elements of a rooftop safety program:
Roof Access
• Identify who should have roof access and to what extent.
• How should the roof be accessed?
– Note all points of access that have been deemed safe.
– Remedy, remove or clearly identify any potential non-safe access points.
Roof Map
• Identify specific concerns related to your building and roof by documenting and highlighting them on a roof map.
– Parapet walls & walking paths
– Emergency egress
– Bad decking
– Fixed ladders
– Roof hatches
– Access
– Skylights
– Other hazards like chemical, respiratory, moving equipment and cell towers, solar panels, necessity to work near a roof edge or opening, etc.
Proper Ladder Usage
• All ladders must be inspected BEFORE climbing.
• Portable ladders can be very dangerous if not set up properly.
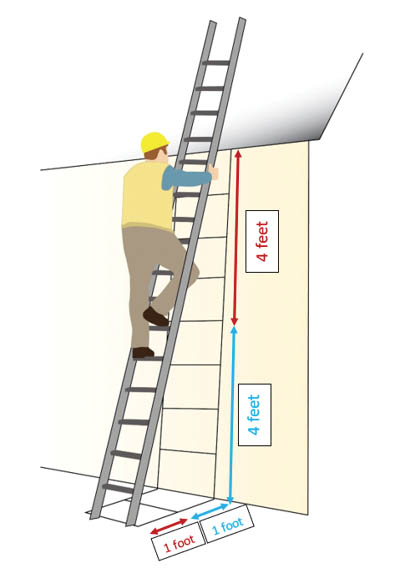
– Ladders should be set up with a 4:1 ratio, meaning for every 4 feet in height, the ladder should be angled out by 1 foot. See diagram at right.
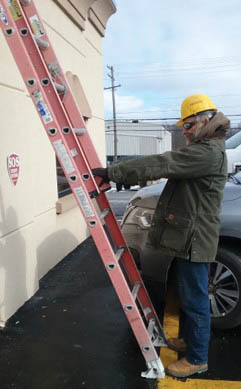
– A good double-check for the 4:1 ratio is the Fireman’s Check. Stand with your toes touching the bottom of the ladder and put your arms out. Your shoulders and hips should be at 90 degrees. See photo at left.
– There should be a minimum of 3 feet of ladder height above the roof edge. This can normally be followed by the Four Rung Rule: making sure there are at least four rungs of the ladder above the roof edge. See diagram.
– Tie off the ladder — best practice is to use a ratchet strap.
– Always make sure the ladder is level.
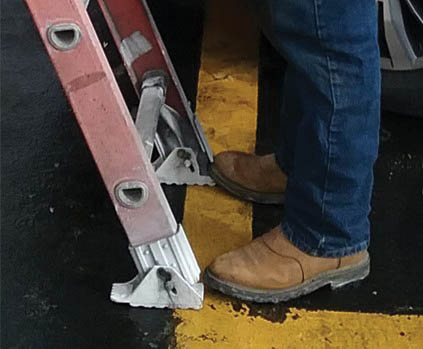
• If you are on a hard surface, such as concrete or asphalt, use the rubber feet to level the ladder (see photo at left).
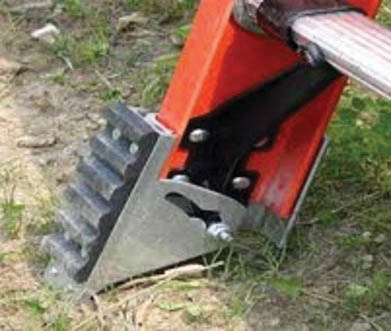
• If you are on soft ground, such as grass, turn the feet down and use the spike to set the ladder into the earth until it’s level (see photo at right).
– Always wear a hard hat when climbing a ladder.
– Maintain three points of contact while climbing, meaning only one hand or foot is lifted at a time. This ensures contact is always maintained with either both hands and one foot or both feet and one hand. See diagram.
– Never carry anything in your hands, even a piece of paper, when climbing the ladder. Use a backpack, tool belt or pocket instead.
Roof Openings: Skylights, Access Hatches & Smoke Hatches
• 10% of all fatalities in the roofing trade are a result of falling through a skylight.
– Skylights, access hatches and smoke hatches should be identified and reviewed from INSIDE the building if ceiling permits viewing.
– Make sure skylights and smoke hatches are highlighted of the roof map.
– Never let anyone coat a skylight or smoke hatch the same color as the roof.
– If possible, install guards around the skylights and smoke hatches.
Bad Decking
• Falls through bad decking account for almost as many fatalities as skylights.
– Depending on the composition, decks can easily be compromised by water. If possible, inspect deck integrity from underneath.
– Remind everyone to look for any signs of bad decking such as indentations, sagging, bulging, water marks from dried standing water, rips, tears, rust or other damage.
– Your program should remind anyone who accesses your roof that if the deck feels soft or makes an unusual sound to retrace their steps and come off.
Other Hazards
• We can often be surprised by other hazards that may be present on a roof. Your plan should include how to safely manage:
– Nesting birds or other wildlife
– Bird waste
– Snakes
– Poisonous plants or insects
– Bees (some people are allergic)
– Homeless individuals
Asking Vendors the Right Questions
When vetting vendors, be sure to ask them about their safety records and programs. The risk associated with not knowing is just too great. Below is a list of questions to consider asking before hiring vendors/contractors to do any work.
• Review the vendor’s certificate of insurance (COI) to ensure that in the event of an injury or fatality, coverages are thorough and adequate. Carefully examine each line item, especially Workers’ Compensation and liability.
• Ask whether they have any employees dedicated to safety, and in what role(s)?
• Utilize internal resources for vendor management to review COI, safety history, policies, procedures and more.
• Ask about their Critical Safety Metrics, which should include the company’s Experience Modification Rate (EMR) and Total Recordable Incident Rate (TRIR) for the previous 3 years.
– The EMR is a reliable indicator of safety performance. It is derived by the insurance industry using a complex formula, including payroll, hours worked and various losses. A figure higher than 1.0 is a debit modification and results in higher insurance premiums. A figure lower than 1.0 is a credit and results in lower insurance premiums.
– The TRIR is a primary lagging indicator of safety performance as the following calculation:
– Number of OSHA recordable injuries x 200,000 hours/actual number of hours worked = number of OSHA recordable injuries for every 100 employees. This works even if the company has fewer than 100 employees because it is expressed as a ratio. As a guide, The Bureau of Labor Statistics (BLS) reports that the average TRIR for commercial roofing contractors is 3.3.
• Ask to review their written safety program, as well as proactive safety programs like new employee orientation, ongoing training, inspection programs, use of technology, etc.
– Are their programs adequate for the tasks they will be performing?
– What methods are used to track and evaluate the effectiveness of their safety program?
• Request a site-specific safety plan. Each building is unique and comes with different safety challenges. For example, a food processing plant will have different safety concerns compared to a hospital.
– If your facility has strict PPE or other protocol, be sure to share details with vendors so everyone is on the same page prior to the start of the project.
Buildings were designed to keep people safe. The most important thing is to make sure anyone who steps foot on your building’s roof is able to complete the job safely that day. Building a documented rooftop safety program, as well as asking the right questions when considering a vendor, can help save you from the hassle and liability from a safety-related incident occurring on your watch.
Stay safe!
— Walter Fluharty, Psy.D, SPHR, CEES, is the senior vice president of environmental health, safety and organizational development at Simon Roofing, where he is responsible for all safety systems and practices across manufacturing facilities and 68 service centers across the United States.