— By Jay Black —
LEDs are the secret to success when it comes to reducing facility costs.
Facility maintenance and management can no doubt be expensive, hence why many managers are left to find options that can help them cut costs and be more efficient with their budgets. Of these everyday expenses, one which offers the most potential for reducing costs is energy — more specifically, lighting. According to Energy Star, approximately 657,000 retail buildings in the U.S. consume more than $20 billion in energy each year. While lighting may only be a portion of this, certain LED solutions offer the potential to impact energy as a whole and general maintenance.
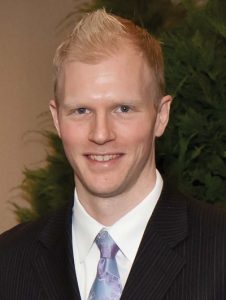
Jay Black
The challenge in getting the most out of your LEDs is in understanding the potential they have and selecting products that will deliver the best quality, longevity and flexibility to meet the specific needs of a facility. While many equate a simple retrofit to initial energy savings, there are a lot more areas of consideration that should be taken into account to ensure you’re maximizing your benefits of your lighting configuration.
Standard Benefits of LEDs
LED lighting provides numerous cost saving benefits that are both immediate and long term. What most people are familiar with is the immediate energy savings that LEDs provide; on their own, LEDs have the ability to reduce energy use by more than 65% when compared to traditional fluorescent solutions. The energy savings are so high that depending on the size of the retrofit project, ROI and payback periods can be as short as only a few years. The savings that follow after this payback period can then be allocated to other areas and efforts throughout the facility — putting money back into the facility manager’s pocket.
ROI is further increased as many LEDs have a significantly longer lifespan compared to other solutions. With a lifespan of up to 100,000 hours, roughly five times that of fluorescent lighting technologies, facilities have the ability to keep the energy savings going much longer while significantly reducing long term maintenance costs that would have been, historically, spent on lamp and ballast replacements. These benefits are reinforced further because of the quality of these LED lights; many LED providers will offer a 10-year warranty, which means facilities are guaranteed a product will last at least 10 years, if not more depending on their frequency of use.
In addition to an increased lifespan, LEDs also provide facilities with increased overall light output and a significant decrease in light depreciation over time, better known as lumen maintenance. After only a quarter of their lifespan, light output from a fluorescent lamp can decrease to only 30% of its original output. In contrast, LEDs typically experience only an 8% decrease in light output over an equivalent time period. While this light output reduces maintenance over time, facility staff can also remain confident that their facilities offer more productive and safer work environments through the LED lighting.
Time and costs dedicated to general maintenance are reduced even further due to the exceptional quality and durability of LEDs, which can be credited to the materials from which it is constructed. Unlike fluorescents, which are made from glass, most LEDs utilize durable plastics, which reduce breakage risks and do not contain mercury or other heavy metals, providing an easily recycled solution compared to fluorescent lighting which requires specialized and more costly methods of recycling.
Greater Control Over Your Energy Savings
The incorporation of various controls, which help to fine tune energy usage and customize the lighting system to a facility’s exact needs, are another LED-integrated option that provides cost and maintenance benefits for facility managers. Lighting controls have the ability to streamline maintenance efforts through smarter facility operation and oversight, can deliver additional savings that easily exceed 10% more energy savings, on top of the 65% offered by just switching to LED.
Over time, lighting controls have greatly increased in complexity, providing a wider range of options from which facilities can choose. The more complex a controls system is, the greater the savings are. For smaller facilities that may not have the budget or simply need a less complex controls solution, there are simple lighting control options such as timers, occupancy sensors and even daylighting sensors that provide simple automation to improve efficiencies. However, for facilities willing and able to take on more complex automation systems, yielding an integrated solution throughout an entire facility or complex would provide even greater detail and control capabilities to maximize potential savings. However, these solutions traditionally come with a higher installation costs and require greater staffing to properly manage over time. Every controls solution is customized to take into account the facility’s budget, location and size; however, there are some controls solutions that have gradually become the standard in retail establishments.
Common lighting controls available in retail spaces will include timers and sensors, particularly used throughout secondary spaces such as backrooms and storage spaces, where lighting is needed much less frequently, particularly during non-business hours. More complex controls such as daylight harvesting can be used in facilities where there is a significant amount of daylight. Even more recent advancements in controls and the capabilities of LED allow for color tuning, or changing of color. This can be particularly helpful when used in display design or certain areas where stores want to focus the attention of customers.
A valuable part of an LED’s controllability is the connectivity the fixtures offer throughout a facility. To more accurately manage lighting systems, internet-based control systems, known as IoT controls, create smart fixtures that provide a more transparent look into facility operations. These “smart” technologies provide real-time information on wattage, broken or burnt out lighting, and other areas of concern. This allows for better management of the facility itself, leading maintenance teams to be as efficient as possible in identifying and addressing issues.
Cutting Costs During High Energy Use Times
Almost any facility will experience peak energy use times that correlate primarily with the seasons. In the winter, retail facilities require longer hours of use for their internal and external lighting technologies as they need parking lots, entrances and other areas of the facility to be well lit to ensure customer safety. In these cases, LEDs provide the aforementioned benefits of greater light output, reduced energy costs and greater controllability for energy savings; however, not all the seasons are as simple.
In the summertime, many facilities need to maintain a comfortable temperature for customers and staff; however, cooling costs to offset temperatures from external heat and increased traffic in the facility can be extremely high. Further adding to the issue, metal halide and fluorescent lighting give off heat emissions that cooling operations need to offset.
Compared to LEDs, fluorescents will generate about 50% more heat in BTUs per hour, and metal halide and halogen lamps will give off as much as 90% more heat in BTUs per hour. This significant reduction in heat generation can have a tremendous impact on HVAC costs throughout a space.
LEDs are a great solution to save facilities on costs, and facility managers should be aware of all the benefits they provide to better understand how they can best be used to minimize costs and streamline efficiency in their establishments. By understanding how LEDs can reduce long term operational and maintenance costs, facilities can take a very significant first step toward developing their own solutions to maximize savings.
— Jay Black is vice president of development and communications for Revolution Lighting Technologies.