— By David Sansenbach —
Protecting power quality is key to restaurant and retail revenue.
One of the most critical elements of running a successful restaurant or retail location is being fully operational whenever you are open to diners or shoppers. In order to do that, electrical equipment like a POS system, a WiFi modem, kitchen printers, security cameras, computing platforms and automation tools need to reliably operate exactly as expected. Given that this equipment is likely quite expensive to purchase (and to fix) and its timely and accurate performance is vital to business continuity, restauranteurs and retail managers should constantly be looking for ways to optimize its performance, extend its lifecycle, reduce operating and maintenance costs, and manage risk. One way to accomplish each of the above objectives is to consider more closely one of the most overlooked and underappreciated elements of facilities operation: the power environment.
Defining the Danger
The term ‘power environment’ refers not only to the quality of the power coming from the grid into the electrical equipment within a given space, but also how that quality varies and what role the equipment itself plays in affecting power quality. When it comes to restaurants and retail locations, the power environments are quite complex, noisy and volatile. This means machinery will be facing a lot of variability in the power it receives.
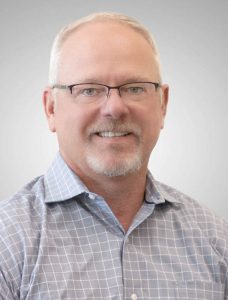
David Sansenbach
Electrical equipment of all kinds relies on a power supply to operate just as a car relies on fuel. Much like fuel, the quality of electrical power varies widely and often in unforeseen ways. Inconsistent power into a machine leads to inconsistent performance out of that machine, and though most folks often believe that power availability equates to power quality, they are mistaken. While the lights being off certainly indicates a power environment has been compromised, the lights being on is no evidence that the power environment (and thus the power in it) is clean.
In fact, it is when the power is on that your systems might be at their most vulnerable. Experts estimate a significant majority of the electrical disturbances impacting the integrity of the power flowing to electrical equipment comes from within the environment itself rather than from dramatic blackouts caused by inclement weather. Such incidents are rare, whereas spikes, normal-mode noise, and common-mode noise are present to some degree all the time.
Seemingly anomalous errors that lead to “no trouble found” service calls are frequently the result of such dirty power disturbances. These mysterious performance issues often result from what is called “disruption,” whereby power disturbances corrupt logic signals, which can alter digital output and lead to software bugs. Other issues include destruction, which is caused by power surges and degradation, which is caused by low-amplitude power disturbances that erode semi-conductors and lead to thermal runaway. These issues can cost your company money in the form of replacement components and additional equipment servicing, and especially downtime. In other words — dirty power translates directly to lost revenue.
Just think what would happen in a restaurant if the POS system shut down. Or the computing systems for online ordering crashed. Unable to charge for completed orders, fulfill existing ones or accept new ones, not only would the customer experience be significantly impacted, but the restaurant also may have to close until the equipment in question is fixed.
From a retail perspective, what if the lights went out? Or the systems on the AV rack crashed? Or the climate control platform failed? A dark, quiet and cold environment is not exactly conducive to the shopper’s experience and could result in temporary store closure. Each of the articulated above are entirely plausible if dirty power is unconditioned, but almost entirely preventable if it is treated.
Securing Your Systems
So what makes power dirty and what can be done about it? For one thing, anything that uses electricity creates noise in some form or another, including the very systems managers are trying to protect. This means POS systems, refrigeration units, HVAC systems, AV products, and even overhead lighting can cause electrical disturbances. To help illustrate how this works in a graphical sense, consider that clean power flows in a sine wave. Power problems appear as sags, swells or spikes in that wave. The more advanced electronics equipment is, the more susceptible it is to even the smallest power disturbances, so these blips are a big deal. As established earlier, inconsistency in power means inconsistency in performance, so keeping that sine wave smooth is paramount.
A solution to maintaining uptime and protecting the equipment within your restaurant or retail location is a power quality management system that will filter electricity flowing from the energy source to each device to ensure clean and consistent performance. Even the most meticulously engineered and carefully calibrated electrical equipment is inevitably impacted by what is put into it, so a power protection solution works similarly to the way a fuel filter protects a car engine from impurities.
Where to Turn
It is worth mentioning, however, that not all power protection is created equal. The three key components that ensure a solid power quality system are a surge diverter, a noise filter and a low impedance isolation transformer. While the majority of solutions available deploy a surge diverter, a noise filter, or both, the most important element of power protection is actually the low impedance isolation transformer. This specialized feature acts to isolate the powered instrument from the power source and reestablishes the neutral-ground bond without opposing or disrupting the current path, keeping unwanted noise out without negatively affecting power flow. This ensures only clean, reliable power consistently flows to and through your devices. Solutions without a low impedance isolation transformer may actually cause disturbances — and therefore downtime — rather than reducing them.
There are a variety of products out there designed to meet the power conditioning needs of restaurants and retail locations, with a few single-solution options out there that enable managers to run every piece of equipment off a single local-area power center. The best place to get information on which option is right for you would be through a professional power quality consultant or an equipment dealer.
At the end of the day, power protection is about proactively mitigating and managing the risk to your equipment (and, therefore, your business) from power-related failures including performance degradation, erosion of sensitive conductors, components, and circuits from low-amplitude power disturbances, and surges. Restaurant and retail franchisees cannot wait for electrical issues to happen because if and when they do, their customers certainly won’t wait around either.
— David Sansenbach is AMETEK Powervar’s national account manager, retail technologies, specializing in providing power quality solutions to the POS industry. Connect with Powervar at: www.powervar.com.
.