— By Adam Kulpa —
How the lowest asphalt bid might cost you more in the long run.
Replacing a parking lot is a huge investment for most property owners. It is also a huge liability when it comes to trip hazards and increasingly stringent ADA regulations. Because of the cost, the inconvenience to the tenants and the liability, it is imperative to invest the time and resources into planning the project properly. Equally important is selecting the contractor that is experienced in dealing with your specific issues.
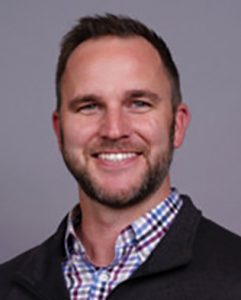
Adam Kulpa, Sunland Asphalt
Not all contractors are created equal. Sometimes selecting the cheapest proposal might end up costing you more in the long run. Here are three tips to help you avoid mistakes that lead to unneeded change orders, wasted resources and time, or, even worse, costly litigation.
Define the Scope Beforehand
Clearly define the scope of the project prior to meeting with the contractor. Many times property owners leave it up to the three contractors that show up to the job walk to set the scope. If you are looking at investing a significant amount of money on asphalt repairs, you shouldn’t leave it up to the three guys you just met to tell you what needs to be done. Establish a relationship and a partnership with a trusted source that can help you set the scope.
If you don’t have time to develop a trustworthy relationship with a contractor, hiring an unbiased third party to determine the scope or work can be worth the fee. Depending on the area, a third party might be an architect of record (AOR), engineer of record (EOR), or a non-bidding, trusted contractor.
Know Your Asphalt
When repairing or replacing existing asphalt, get core samples and/or a geotechnical engineering report. Core sampling your parking lot can save you thousands of dollars in unforeseen change orders. Core sampling is a process where a 12-inch hollow drill bit drills into sections of your parking lot and removes material. The cross sections of asphalt are examined, showing the thickness, number of layers and strength of the materials. This information is key when doing remove-and-replace repairs and mill-and-pave projects.
Contractors use their best judgement when estimating projects. But without a history of work done or core samples, they are guessing what is underneath the top layer of asphalt. It isn’t until they are mid-project, with asphalt removed and equipment on-site, that they find the current parking lot is 6 inches deep instead of the 3 inches deep they quoted. An alternative to core samples is to budget a percentage for change orders into milling and paving projects.
Qualify Your Contractor
Find a partner — not a contractor — and develop a working relationship with them and their firm. Ask questions about their safety rating, if they are bonded and insured, current legal matters, how billing works, and what kind of service can you expect. Look up their license number within the state registry. Ask what their current workload looks like, if you get a dedicated account manager and team, how many locations can they effectively help you manage, and how much of their work is subcontracted.
Asphalt repair and maintenance is an investment in your property, business and sanity. Top tier contractors should be helping you free up your bandwidth with great communication, professional proposals and excellent workmanship. Often, these intangible attributes are worth more to busy facility managers than the cheapest proposal.
— Adam Kulpa is the national accounts manager for Sunland Asphalt, a national paving company that operated in 38 states in 2018 and has 550 employees. Sunland specializes in reactive maintenance work and large-scale capital projects. For more information, visit http://sunlandasphalt.com.