— By Steve Tudhope —
AutoZone goes the extra mile to reduce energy usage and drive the future.
Memphis, Tennessee-based AutoZone is the leading distributor of automotive replacement parts and accessories with more than 6,200 retail stores in the United States, Puerto Rico and Mexico. In 2003, AutoZone’s corporate leaders challenged its maintenance team to research the drivers of store utility expenses and find ways to reduce energy costs without detracting from the store environment. AutoZone’s primary objectives were to:
- Improve energy efficiency and reduce energy usage and costs.
- Develop and maintain effective monitoring, reporting and management strategies for wise energy usage.
- Find new and better ways to increase returns from energy investments through research and development.
- Reduce the impact of curtailments, brownouts or any interruptions in energy supply.
Energy management systems were not a new concept. However, those that existed in the early 2000s were designed specifically for big box retail stores and large commercial buildings. AutoZone tested several of these legacy systems in its stores but found that they were too expensive and lacking the features it needed. Having already upgraded its thermostats, AutoZone next wanted to custom design an energy management system that would work for its small box retail stores.
In its quest to create a custom system to remotely manage and control energy usage at its retail stores, AutoZone became a pioneer of energy management for the small box retail category. Its maintenance team collaborated with engineers to develop, test and pilot an energy management system. An early adopter, AutoZone was one of the first small box retailers with the ability to remotely monitor and control the HVAC and lighting equipment at its stores.
Funding: $1 Million From the California Energy Commission
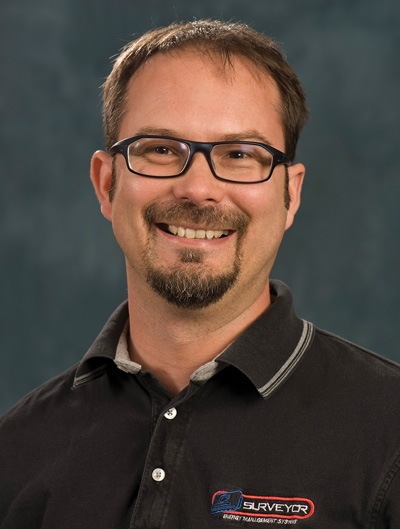
Steve Tudhope, Venstar
In 2003, AutoZone did a comprehensive test of the new energy management system in 26 of its California stores. The test was successful, significantly reducing energy costs at these stores. AutoZone’s leadership team was so pleased with the energy savings that it rolled out the system to all of its stores in California (380 at that time).
AutoZone was able to take advantage of the California Energy Commission’s 2003 Cash for Kilowatts program that tested and validated energy savings capabilities. It validated AutoZone’s ability to comply with demand-response incidents by remotely controlling lighting and HVAC to reduce energy usage. As a result of AutoZone’s proven energy savings systems, the commission awarded AutoZone $1.1 million to subsidize its investment in this new technology.
With the cost-saving success of the energy management system along with the rebate, AutoZone’s leadership team authorized the installation of energy management systems at all of its stores in the U.S., Mexico and Puerto Rico.
How It Works: An Inside Look at the AutoZone EMS
AutoZone’s energy management system consists of controls and sensors that are installed in each HVAC unit to monitor its efficiency and help manage the health of the equipment. Lighting/load control panels independently control interior and exterior lighting zones, including parking lots and outdoor signage. Interior occupancy sensors turn lights on and off in areas of the stores that are not frequently used.
An ultra-secure Internet gateway transmits data from each store’s HVAC and lighting equipment controls and sensors to the corporate data center. All of the equipment can be remotely managed using a desktop computer or via the mobile app. For select stores, AutoZone also installed an energy-monitoring device that provides insights on the total power usage and monitors individual circuits.
AutoZone’s energy management system controls the energy usage at more than 6,200 AutoZone stores in the United States including Puerto Rico as well as Mexico, where it has more than 500 stores. Across the chain, the system manages more than 20,300 HVAC units and more than 6,100 electrical lighting control panels with more than 200,000 sensors. AutoZone stores typically have two to four rooftop HVAC systems. Most stores, which are an average of 7,000 square feet, have peak loads of 30 to 60 Kilowatts per month.
Remote Monitoring & Control of HVAC & Lighting
A key benefit of AutoZone’s energy management system is the ability to remotely monitor and control the HVAC and lighting equipment. More than 150 field personnel, including AutoZone’s energy management, maintenance and corporate construction teams, rely on the mobile app to remotely monitor and make changes to the HVAC and lighting equipment at the stores from virtually anywhere.
For example, if a store manager reports that the store is too hot or too cold, the energy management team can check temperatures and make remote adjustments from a desktop computer or from a mobile device. In addition, they use the system to ensure that interior lights are not left on overnight and that parking lot lights are not left on during the day. They can also remotely validate repair work that is being done on the electrical and HVAC equipment.
“Global Changes” Feature Enables Simultaneous Modifications for All Stores
A key advantage of remote management is the ability to make global changes. Instead of having to manually make changes for each of the more than 6,200 stores, the energy management team simply chooses global changes to make simultaneous modifications for all stores or for stores in a select geographic region or climate zone. For example, if there is a change in the stores’ hours, it takes minutes instead of hours or days to update the equipment schedules for stores in a select region or for all of the stores.
Emergency Alerts Enable Immediate Action, Fewer Truck Dispatches
Daily summary exception reports let the team know when store systems deviate from pre-set temperatures so they can immediately check to see if there is an issue with the equipment or some other problem. Additional alerts can advise if there are any urgent situations, such as if a store loses power, so immediate action can be taken.
Preventive Maintenance Helps Prevent System Failure
The energy management system also helps with preventive maintenance. For example, if the supply air is not within the pre-set temperatures, the system sends an email alert to the designated management team members, advising them there may be an issue. This allows the energy management team to know exactly which HVAC unit is not performing properly so they can take care of issues before they become costly problems. Having remote access to diagnose and troubleshoot issues also results in reduced costs by eliminating unnecessary maintenance truck dispatches.
System Over-Ride to Accommodate Changes in Store Hours
Each store has programmed HVAC and lighting settings and schedules based on store hours, which helps ensure that the heating, cooling and lights are not left on when the store is unoccupied. Since store schedules vary for store maintenance, inventories and deliveries, the system also includes the option to over-ride the pre-set program.
Visual Reporting on a Big-Screen Monitor
At the AutoZone corporate offices, visual reporting is accomplished using a big-screen monitor that shows the status of every store displayed on a map, which includes local weather. This feature of the energy management software allows the team to make necessary adjustments in real time to keep stores comfortable, especially during extreme temperatures.
Participation in Utility Demand-Response Programs
AutoZone’s energy management system includes a demand-response manager. Participating in demand-response programs allows AutoZone to help utilities avoid brownouts by reducing or shifting energy usage during peak periods. This also allows AutoZone to take advantage of time-based rates and financial incentives offered by the utilities.
Additional Energy-Saving Measures That Help Cut Energy Costs
To take advantage of further opportunities to reduce energy costs at its stores, AutoZone’s energy management team has implemented creative solutions to common problems, including:
- Alerts for backup generators. In Puerto Rico where energy can be unreliable during storms or power surges, the stores rely on backup diesel generators. Alerts let AutoZone’s energy management team know when the generators need fuel so that the stores can stay operational.
- HVAC equipment planning. Using data on the run times of the HVAC equipment enables the construction team to make educated decisions about the number and size of units needed for the different sizes of stores. This helps reduce costs and improve efficiency.
- Factory-installed energy management controls. AutoZone was a pioneer in working with leading HVAC manufacturers to factory install energy management controls and sensors into their equipment, making it faster and easier for installation.
Extensive data mining, diagnostics and analytics capabilities also help the energy management team identify areas of additional energy savings.
Going the Extra Mile to Save Energy
Taking a broad approach to reducing its energy load, AutoZone’s energy management team utilizes additional technologies to improve energy efficiency, including:
- LED lighting: AutoZone has converted all of its stores from fluorescent to induction lighting or LED lighting. Moving to LED has resulted in millions of dollars in savings annually plus reduced handling and inventory costs.
- Daylight harvesting: For select stores, AutoZone takes advantage of “daylight harvesting,” which dims the interior lights in direct response to sunlight coming in through the windows.
- Energy-efficient roofing: AutoZone transitioned from traditional roofing to highly reflective roofing material that reduces interior temperatures and energy consumption by as much as 30%.
AutoZone also uses oil additives to reduce motor friction and improve HVAC system efficiency. Weather sealing the store doors also improves energy savings.
Looking to the Future
AutoZone continues to stay at the forefront of energy management by piloting new technologies. In fact, it recently implemented a pilot program for solar-assisted HVAC. Solar collectors take over a portion of the HVAC compressor’s workload by providing thermal energy to the refrigerant, reducing energy consumption of the RTUs. This results in reduced energy consumption and increased energy efficiency, delivering lower operating costs. AutoZone’s solar-assisted test store reduced 86,558 pounds of CO2 per year.
Success in Meeting AutoZone’s Environmental Responsibility Goals
The energy management system has met AutoZone’s goal of reducing energy usage while maintaining comfortable store temperatures and proper lighting. It also helps AutoZone meet its ongoing environmental responsibility initiatives, including:
- Reducing energy usage and costs.
- Reducing HVAC run times.
- Remotely monitoring and controlling HVAC and lighting at all of the stores.
- Managing store lighting with occupancy sensors, time schedules and daylight harvesting.
- Utilizing analytics to identify potential opportunities for energy savings.
Overall Results: $167 million in energy cost avoidance
Since 2007, AutoZone’s energy improvement strategy has resulted in reduced energy usage of more than 1.35B kilowatt hours, resulting in millions of dollars in energy cost avoidance through its fiscal year 2018. In addition, AutoZone currently saves an average of 30% annually on its energy costs compared to not having an energy management system, resulting in a savings of millions of dollars per year.
As well, AutoZone aggressively pursues all available state and utility rebates for energy saving projects.
As a result of the success of the program, the energy management team was recognized by AutoZone’s corporate leadership for its contributions over the past 15 years. The team was honored for evolving the AutoZone Store Energy Savings initiative, from rolling out an energy management system to creating a long term strategy for developing strategic enhancements for its energy management for 2019 and beyond.
— Steve Tudhope is a vice president of Venstar Inc., which provides energy management solutions to the biggest names in small box restaurant and retail chains. Venstar’s Surveyor EMS typically saves small box retailers 20% to 35% of their energy costs, which translates to tens of millions of dollars in savings each year and dramatic reductions in CO2 emissions. Surveyor currently controls the energy usage of 30,000+ retail locations across the United States, Canada, Puerto Rico and Mexico.