— By Kevin Piel and Joe McMenamin —
Choosing the best insulated-panel system is paramount in ensuring optimal climate-controlled operation in many different applications.
The days when grocery shopping was solely an in-person, on-site event that involved the maneuvering of a shopping cart (wobbly wheel optional) through a maze of aisles featuring shelves stocked with a wide array of goods have come to an end. Technological advances had already begun to make grocery shopping from home much more accessible and appealing in recent years. Then came March 2020.
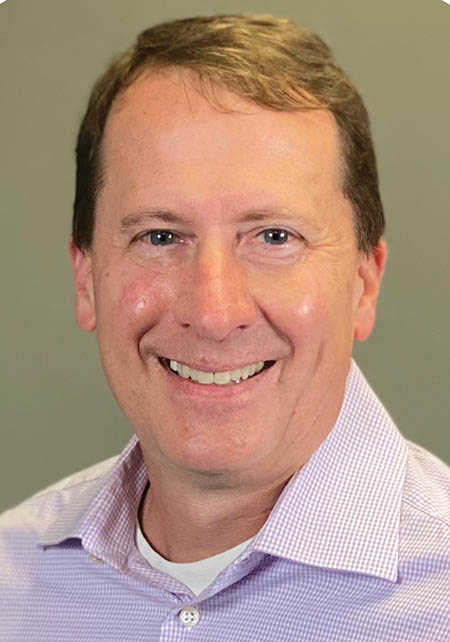
Kevin Piel, Director of Business Development, KPS Global
The COVID-19 pandemic, complete with its lockdowns and stay-at-home orders, was a huge boost for the shop-from-home market segment in all industries. In the world of the supermarket, this phenomenon was called Online Grocery Pickup, or OGP. The main goal of OGP is to make sure that an online grocery order is filled for the customer in a timely and accurate manner, while not compromising food safety. Therefore, the physical pickup site must feature a climate-controlled cold-storage infrastructure that meets all the order accuracy, on-time delivery and food-safety demands of the customer.
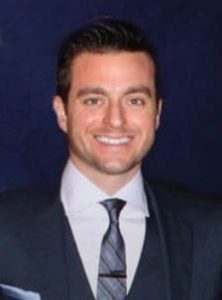
Joe McMenamin, Director of E-Commerce, KPS Global
The main challenge in developing an effective OGP cold-storage system is that there is no one-size-fits-all answer for the unique physical infrastructure and footprint that each retrieval site possesses. Therefore, the companies that create climate-controlled cold-storage solutions for various OGP formats understand that managing and providing different cold-storage temperature levels are the foundation for a successful operation.
The most basic OGP operation must have some form of cold storage to hold the groceries selected from the store for either customer pickup or delivery. More complex or larger OGP operations may need backroom storage coolers and freezers, assembly-line automation systems and even robotic automation that can optimize the order-filling process. Additionally, there may soon come a day where grocery shoppers will not only be able to retrieve their orders by driving up to the store or hopping inside to collect them, but also at co-located sites or offsite like, for instance, at a nearby shopping mall.
In this case, the order-storage solution may need to be suitable for use in outdoor environments that can, depending on the location, experience extreme swings in temperature and climactic conditions. The offsite locations will also have to be fully (and reliably) automated since there won’t be a staff member available to assist with any questions or difficulties.
Answering The Call
In most cases, the OGP operation will need walk-in coolers and/or freezers to keep the purchased products at their proper temperature before they are picked up.
Our insulated panel systems employ a modular-design approach that makes the storage units highly adaptable and easy to install, whether a single- or multi-compartment unit is required. Each system is custom designed and engineered in house to meet the unique specifications of the end user’s project.
The innovative design system features two insulating panels constructed of an exterior metal skin that is sandwiched around poured-in-place closed-cell polyurethane foam. This method of design and construction creates three main benefits for the user:
- The insulated panels are highly energy-efficient and have R-values (the ability to resist invasive energy flow) that are not only relevant to the specific project, but meet or exceed industry standards.
- Closed-cell polyurethane foam has the highest R-value of any insulation used in the refrigeration industry and is able to produce an R-value of up to 8.06 per inch of thickness.
- The insulated panels are outfitted with a cam-lock system that enables them to be securely joined together via a cam-and-pin housing assembly that both forms a sturdy, unbreakable connection between individual panels while operating the system’s R-value.
In other words, insulated panels are an ideal choice for food retailers who have built or are contemplating adding an OGP operation.
That’s Not All, Folks
While OGP is responsible for the most obvious expansion of the insulated-panel market in recent years, the truth is that climate-controlled cold-storage systems have been used for many years in a wide range of applications beyond the typical retail-grocery or foodservice niches. Four of these areas stand out as being ripe for the need for customized walk-in cooler/freezer or equipment-enclosure systems that can benefit from being outfitted with insulated panels. Let’s take a closer look at each:
- Controlled Environment Rooms (CER): These structures are most commonly used as chambers for testing things such as electronic products or automobile tires. The operators of CERs will build the room, put in a heating/cooling/humidity unit and then manipulate the atmosphere to see how a product — for example, tires — will perform under the stress of changing temperature and humidity conditions over thousands of test cycles. Because of this, CERs need to be weather-tight and the insulation must deliver a high R-value. Insulated panels can satisfy those operational demands because, while they are not waterproof, they are moisture-tight so that they can maintain the required environment during the full range of the testing process.
- Stability Chambers: Stability Chambers are similar to CERs, but are generally used in the production of pharmaceuticals, healthcare products and cosmetics. Common cold-storage applications in this realm include scientific chambers, clean rooms, lab rooms, dry rooms, pharmaceutical testing and vaccine storage. On the pharmaceutical side, all of the manufacturing processes must take place in facilities where the conditions are monitored very closely and have extremely tight operational tolerances, as laid out by the U.S. Food & Drug Administration (FDA). In many scientific applications, the insulated panels are required to be constructed of metal due to concerns that any moisture that finds itself in contact with the wood rails can lead to mold and bacteria growth. This is a requirement that can be satisfied through the ability to construct panels from different types of metals, including stainless steel and aluminum.
- Grow Rooms: These structures typically fall into two categories. The first type of Grow Room is used for testing biological materials that may be used in the development of various other products. The other use is for creating the optimal growing conditions that will improve a plant’s rate of growth, such as in vertical farming. This has also become a, pardon the pun, “growing” market niche as more and more states are legalizing the use of cannabinoids in the manufacture of medical products and recreational consumables. Grow Rooms don’t typically need to have high R-values, so the main benefit of insulated panels in these applications is their ability to be fashioned into a finished growing space faster than one that is constructed of metal or sheet rock. The panels are also easy to clean and are available with different finishes, such as stainless steel or aluminum.
- Equipment Enclosures: As their name implies, these facilities are used to enclose equipment, most notably in the power generation/transmission, oil and gas, water/wastewater, petrochemical and renewable-energy industries. The companies that operate in these industries build large skid-based systems that are often the size of a shipping container. An insulated-panel system is then constructed around the skid so that the equipment is protected from the elements, while an integrated heating/cooling system is used to produce and maintain the unit’s interior atmosphere with regard to temperature and humidity levels. In some instances, the panels used in Equipment Enclosures must meet a predetermined fire-suppression rating.
Conclusion
In all of these applications, insulated panels are setting the standard for highly reliable, efficient, safe and cost-effective performance because the unit can be designed, engineered and built to the customer’s customized dimensions.
— Joe McMenamin is the director of e-commerce and Kevin Piel is director of business development for KPS Global, Inc., based in Fort Worth, Texas. They can be reached at [email protected] and [email protected]. KPS Global®, Inc., is an industry-leading manufacturer of insulated panel systems that are designed for use in creating climate-controlled cold-storage systems.