— By Kyle Klahre —
The world of refrigeration is rapidly changing — here’s what grocers need to know.
Refrigeration systems in the U.S. are rapidly evolving due to new government regulations affecting residential, commercial and industrial systems. To understand current changes, it’s helpful to look back at the history of refrigerant regulation. This regulatory journey can be traced back to the middle of the 1980s. The Baby Boomer and Generation X readers likely remember hearing NASA discovered a hole in the ozone layer over Antarctica. Well, the cause of this alarming discovery was eventually attributed to many of the refrigerants, aerosols and foams we were using in our everyday life. Specifically, it was the substances that had a chemical composition containing chlorine as they would react with ozone molecules once released into the atmosphere. This led to the 1987 Montreal Protocol, an international treaty to phase out these substances with ozone depletion potential (ODP).
Refrigerants such as R-12 and R-22, often mistakenly generalized as the brand Freon®, were set to be phased out over the coming years. The industry shifted to hydrofluorocarbon (HFC) refrigerants and blends with zero ODP, such as R-134a, R-407A, R-410A, R-448A and R-513A. These fit into existing or similar systems with minimal rework. However, not all that glitters is gold as these refrigerants still came with a high global warming potential (GWP). In 2016, the Kigali Amendment to the Montreal Protocol looked to counteract this by setting a plan to gradually reduce the consumption and production of HFC refrigerants. Although the ratification of this amendment was met with hesitation in the U.S. originally, the U.S. federal government aligned with this amendment at the end of 2020 by signing into law the American Innovation and Manufacturing (AIM) Act.
That brings us to today. The AIM Act set a schedule to phase down the use of HFC refrigerants in the U.S. market while also empowering the U.S. EPA to develop regulations to meet this schedule. Thus far, the EPA has established supply restrictions, sector-based GWP limits, and standards for servicing and repair of existing systems. Although all sectors will see this impact in their business one way or another, the retail grocery sector is an increasingly interesting yet challenging one (see Figure 1 for important regulation information for grocers).
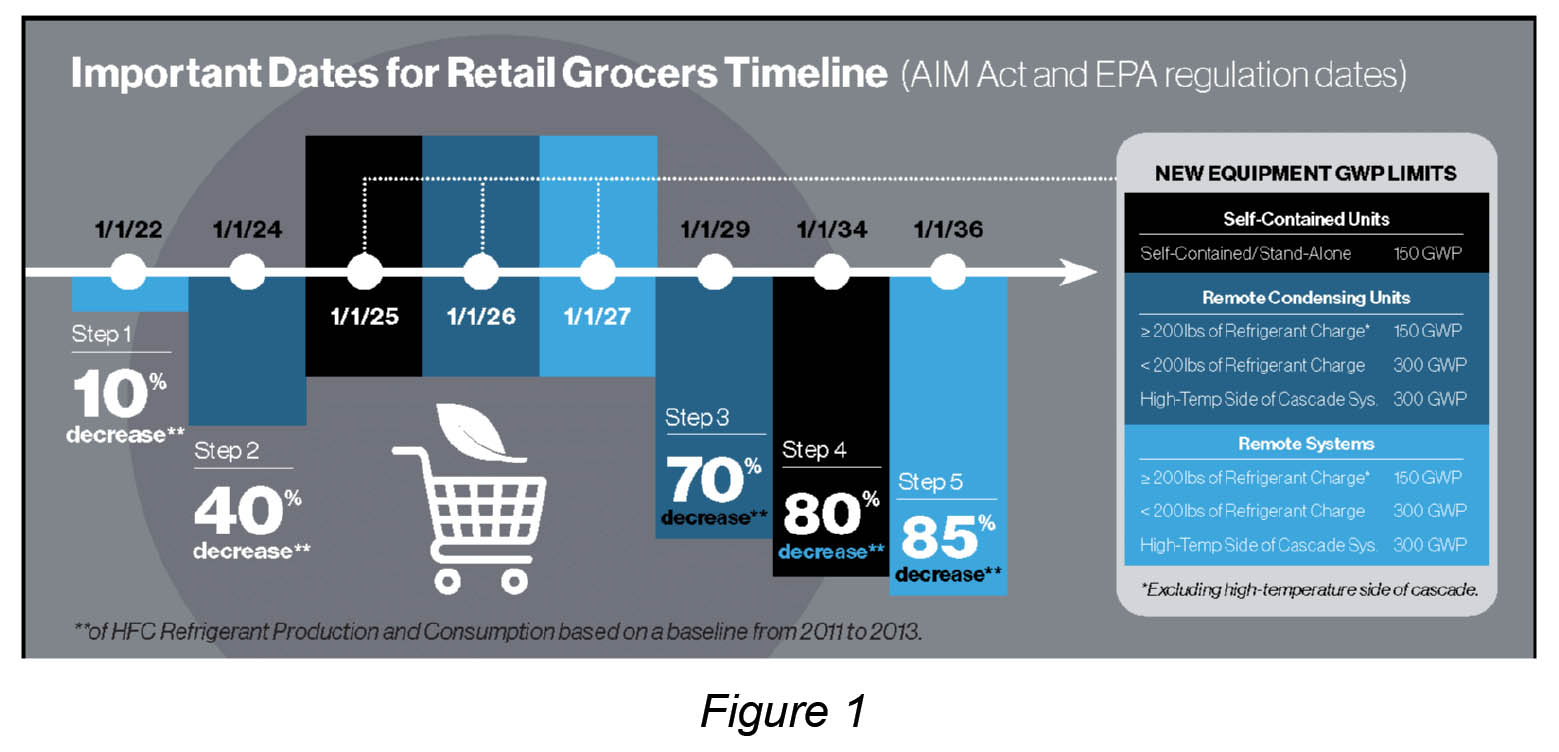
What makes the retail grocery sector so interesting is the nature of the industry itself. The supermarket industry sees low profit margins (usually 1% to 2% of sales). Additionally, supermarkets are the most electricity-intensive type of commercial building due to the need to keep food cold. The refrigeration system within the supermarket is on average the biggest energy user, accounting for about 40% to 60% of electricity consumption. Most of these refrigeration systems rely on high GWP HFCs making them a target to AIM Act regulation. In the retail grocery sector, the AIM Act is introducing unfamiliar systems, increasing operating costs of existing “non-compliant” systems, and impacting grocers’ profits. All current leading future-proof systems require major components to be replaced and often suffer efficiency losses. In short, this regulation poses significant risks for grocers. The risk of misunderstanding the complicated current and future regulations. The risk of spending money on wrong technology based on application and climate. The risk of having a system that their maintenance team is unfamiliar with. It is more important than ever for grocers to remain educated on regulation and potential solutions for their specific situation as it is no longer one-size-fits-all. So, what could the future look like?

One system that is certain to be part of the future of supermarket refrigeration systems is a Transcritical CO2 booster system (TCO2) (Figure 2). The TCO2 system uses CO2 (R-744), a non-flammable, low toxicity refrigerant with a GWP of 1, making it a future-proof solution. It serves both low and medium temperature fixtures, reducing the number of systems needed. However, efficiency drops in high ambient conditions due to CO2’s critical point at 87.8°F and 1056 PSIG. The system also requires additional components like high-pressure expansion valves and flash tanks, which add complexity and cost. Innovative solutions like ejectors and subcooling can help regain some of these energy inefficiencies but also increase complexity and cost.
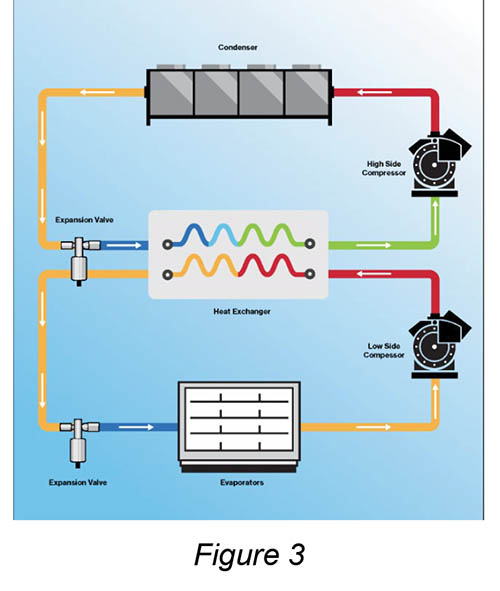
The main issues for TCO2 systems are their performance in hotter climates. Unfortunately, installing it in colder climates isn’t feasible for much of the U.S. A solution to this is a cascade system where CO2 serves fixtures but is always condensed well below its critical temperature by a high side (non-CO2) system (Figure 3). Another option is pumping CO2 as a saturated fluid where a high side (non-CO2) system maintains the temperature of the CO2 while condensing any evaporated CO2 back to liquid. Despite ongoing regulatory challenges regarding the high side refrigerant, these systems are likely an intermediate step for many grocers. They reduce the amount of higher GWP refrigerant at a store, use CO2 where it is most efficient, and allow for vetting of future refrigerant options.
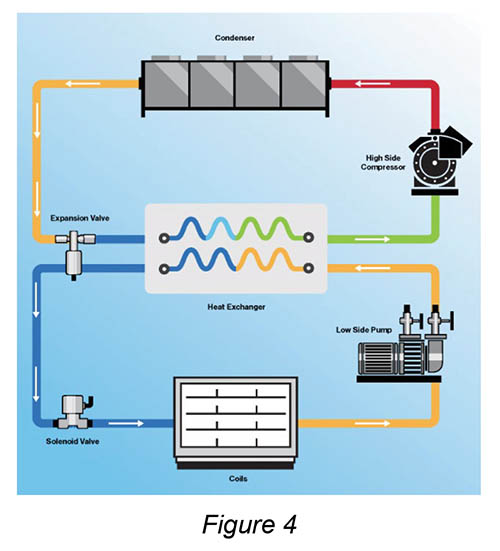
While CO2 will be a solution for some grocers, it won’t be the only one. Many grocers hesitate to transition to CO2 due to the added complexity, volatility and higher operation pressures of the systems. Another solution is a glycol chiller system (Figure 4) where we can utilize a similar high side/low side setup as mentioned above, but instead of pumping CO2 we pump a water/glycol fluid. This system will still face regulatory challenges on the high side and it will be limited to medium temperature applications as the concentration of glycol necessary for freeze protection at low temperature applications makes the fluid very difficult to pump. Self-contained fixtures using propane (R-290) or other hydrocarbons may find their niche here. These fixtures will each have their own compressor systems. Some grocers may lean toward installing these on a pumped condensing water loop to avoid releasing all the heat inside the store — resulting in extra load on the HVAC system. Despite low GWP, flammability concerns and higher costs may limit these to low temperature applications within stores where a glycol chiller system is used on medium temperature applications.
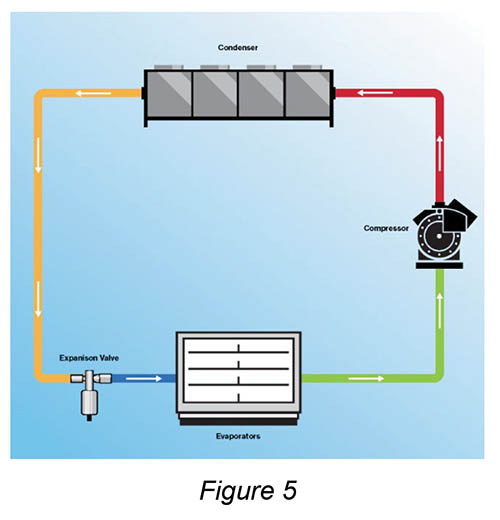
All previously mentioned systems face their own set of challenges while also adding complexity compared to existing HFC systems. A standard direct expansion (DX) system using A2L refrigerants can simplify designs for grocers (Figure 5). Familiar to technicians, these systems meet regulatory GWP limits and are conventional in most ways. They avoid complex designs and efficiency penalties seen in other systems. The caveat? A2L refrigerants are mildly flammable and thus require additional safety mechanisms. Similar to previous systems, they can’t be retrofitted into existing HFC systems without replacing all major components. These hurdles are minor overall especially compared to the previous systems’ lists of challenges. However, the biggest challenge immediately for widespread use of A2L refrigeration systems is local jurisdiction adoption. In the long run, they could become an excellent solution as the primary side of a secondary system or in a standard DX refrigeration system, which we are all familiar with today.
The evolution of refrigeration systems in the U.S. is driven by regulatory changes aimed at reducing environmental impact. The AIM Act and EPA regulations push the market toward sustainable solutions, but this transition comes with its own set of challenges. Grocers, in particular, face the daunting task of navigating these changes while maintaining profitability and operational efficiency. As the industry moves forward, it is crucial for stakeholders to stay informed and adaptable, exploring various refrigeration technologies to find the best fit for their specific needs. The future of refrigeration will likely be a blend of different systems, each with its own advantages and trade-offs, but all contributing to a more sustainable and environmentally friendly market.
— Kyle Klahre serves as project engineer for Cuhaci Peterson. He is an experienced professional engineer and certified energy manager in the commercial refrigeration and HVAC industry. With experience in leadership and team development, he has a proven record of producing unique sustainable design solutions to drive cost savings while meeting the evolving regulatory demands of the supermarket industry. Email the author at [email protected].