— By Bryan Campbell —
When developing on potentially contaminated property, you can protect your new building from VOCs with a vapor barrier.
Historically, the term “vapor intrusion” was discussed only in association with the most heavily contaminated properties. Now, with the emergence of new stricter guidelines, the United States Environmental Protection Agency (EPA) and many state regulatory agencies identify vapor intrusion as a major driver on many sites, including those with little to no soil or groundwater contamination. In some cases, potential vapor intrusion is not related to the subject site but rather results from contamination migrating from a nearby property. This is particularly common in dense urban settings where sources of volatile organic compound (VOC) contamination such as dry cleaners, gas stations and industrial operations are prevalent.
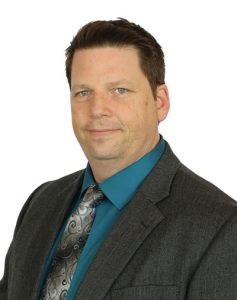
Bryan Campbell, Partner Engineering and Science, Inc.
Vapor intrusion is no longer an emerging science and is now a well-established pathway whereby environmental contaminants (VOCs) can enter an existing structure and potentially results in health risks to building occupants. Similar to radon, VOCs can enter a structure via the ground floor or subterranean levels. VOC trichloroethylene or trichloroethene (TCE), a VOC commonly found at former dry cleaners and some industrial properties, has potential for fetal heart defects. The vapor intrusion risk for the VOC is more urgent, and the EPA and some state agencies have established short term exposure guidelines. Per EPA guidance followed by many state and local agencies including the Department of Toxic Substances Control, a building owner must act within days or weeks of becoming aware of the contamination. Identifying and mitigating a vapor intrusion issue after a building is constructed can be a time-consuming and expensive proposition.
Designing and installing a vapor intrusion mitigation barrier during construction can reduce or eliminate the threat posed by vapor intrusion. A vapor barrier can increase the value of a building and reduce liability.
Implementation of a vapor intrusion mitigation barrier typically consists of the following components:
- The vapor barrier design, which is a set of engineer design drawings prepared by a qualified environmental engineer and provided to the general contractor to construct the vapor barrier via a certified applicator familiar with the installation of the recommended barrier;
- The vapor barrier, which is typically composed of a low-profile sub-slab vent array installed within permeable aggregate that is overlain by the vapor barrier (sheet roll) composed of one to several layers of chemically resistant material that is sealed around utility penetrations and between sheets using barrier specific sealant materials; and
- Performance of quality assurance/quality control program, including smoke testing to verify sealing, and sometimes thickness testing.
The site-specific analysis is often necessary to develop appropriate mitigation measures for vapor intrusion because many available barrier products do not effectively mitigate vapor intrusion by VOCs. When in doubt, always consult with an environmental professional who fully understands product specifications as well as your project needs. Qualified vapor intrusion mitigation specialists will be able to assess your project and provide preventative and mitigative solutions, while supporting your objectives.
Here are a few common questions and answers regarding vapor intrusion and vapor barriers:
- I have a moisture (water vapor) barrier beneath my building so am I protected from vapor intrusion?
No. A moisture barrier is for water vapor and is not the same as a VOC vapor mitigation barrier. VOC vapor barriers are designed with materials and procedures specifically designed for VOC vapor mitigation. A moisture/water vapor barrier alone will not stop the risk of VOC vapors entering the building.
- There was an old dry cleaner on my property, but that was years ago and the contaminants cannot still be there, can they?
Studies have shown that over 70% of dry cleaners have contamination that can remain for decades, long after the dry cleaner has ceased operations. The remaining or residual contamination can include TCE and other VOCs that pose a risk to existing and/or future structures.
- I noticed a dry cleaner right next to my property; can I just take some samples of the air inside my building to see if there is a vapor intrusion problem?
Collecting one round of indoor-air samples will provide a snapshot in time of indoor air conditions; however, without understanding the magnitude and extent of contamination beneath, and in the vicinity of the existing or planned building, the potential for vapor intrusion will not be known. Additionally, indoor air concentrations can vary seasonally and over time because vapor intrusion is influenced by several factors including atmospheric pressure and weather conditions. Therefore, just because indoor air contamination is not identified now, does not mean there will not be exceedances when sampled in the future.
- If I have a vapor intrusion problem, can I just open the doors or run some fans inside of my building?
This may seem like a good idea; however, this approach will not mitigate the vapor intrusion issue long term, and most buildings cannot have the doors open all the time due to seasonal changes and associated energy expenditures.
- Can I just construct my building now and deal with any vapor intrusion problems later?
Yes, but it will cost much more to deal with a vapor intrusion problem after construction versus installing a vapor barrier during construction.
- I am constructing a building, but my GC has no idea how to install a vapor barrier or what materials to use. What should I do?
It is advisable to consult with a well-trained and qualified team of specialists for vapor barrier design including the selection and application of the materials, testing and inspections.
— Bryan Campbell, PG, CHG is senior project manager with Partner Engineering and Science, Inc., which offers full-service engineering, environmental and energy consulting and design services. Partner serves clients from initial due diligence and design to development and construction, as well as the ongoing maintenance and optimization of a real estate asset. For more information, visit www.partneresi.com.