— By Jason Roeder —
Advancing restaurant and retail sustainability: the power of equipment data.
Last March, the Securities and Exchange Commission (SEC) proposed new rules that will impact every publicly traded multi-unit retailer or restaurant. If the regulations are adopted, these organizations will have to disclose their greenhouse-gas emissions, climate goals and the effect of climate risks on their businesses.
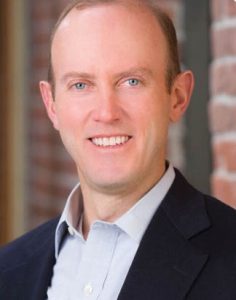
Jason Roeder, Powerhouse Dynamics
This development adds a new level of urgency for these sectors, which are already working to reduce their carbon footprint. It’s far from easy; a previous study cited by ENERGY STAR found that retail buildings incurred the highest portion of energy costs of all commercial facilities in the US. ENERGY STAR has also noted that restaurants “use about five to seven times more energy per square foot” than other commercial structures.
Maintenance, facilities, operations and other managers have tremendous power to make a difference by better managing their energy-intensive equipment across their portfolio of sites. Their actions can directly impact their businesses’ financial performance, daily operations and brand reputation. Technologies such as the Internet of Things (IoT) give them more control to reduce their carbon footprint than was previously possible.
These technologies enable managers to accomplish two objectives: (1) lower/optimize the consumption (and costs) of energy and resources, such as heating, air conditioning, electricity, gas and water, and (2) make better equipment repair/replace decisions to support sustainability goals.
Getting Connected
The first step in this process is to connect this equipment — such as HVAC, signage, lighting, doors, freezers, refrigerators, ovens, fryers, dish machines, exhaust hoods and more — either digitally or through sensors. From there, it becomes easy to monitor, analyze and automate it through a mobile device, and start to deliver improvements. Simple measures such as preprogramming air conditioners to run on a synchronized basis — rather than simultaneously — can reduce stress on the grid and cooling costs.
For managers who are just beginning this process — or scaling it up — the insights IoT provides can be eye opening. It is very common, for example, for a connected facility to reveal problems with HVAC equipment that were previously undiagnosed.
The Impact of Supply Chain Interruptions
Today, supply chain interruptions are another factor to consider in managing energy and achieving more sustainability. For example, if heating or cooling equipment suddenly breaks, management may be forced to accept whatever their supplier has at the warehouse, regardless of its level of efficiency.
Contrast that with the proactive, strategic approach IoT allows. Managers can evaluate and make changes to their equipment fleet based on the data their connected equipment transmits and their utility bills, the age of the machines and other factors. If the data shows some pieces of equipment struggling to reach a certain temperature, management gains more insight for repair/replace decisions.
A clothing retailer, for example, can schedule the replacement of air conditioners that are high in ozone-depleting refrigerants based on their run time, energy usage, how quickly they’re achieving their targeted temperatures, and other measures hidden in the data.
In some cases, management might choose to replace old but functional equipment with newer models that are far more efficient. In other cases, they might identify machines that should be proactively repaired to maximize their performance, avoid costly replacement and keep them out of landfills.
Planning for Peak Demand
During peak heating and air conditioning season, IoT can reveal insights in time to make a difference. With the competition for in-store traffic, for example, it’s not uncommon to find staff keeping outside doors open — even when it’s very cold or very hot out. When the doors are connected, it’s easy to detect deviations from standard company protocols.
As stores prepare for the holidays, they can evaluate their HVAC units and ensure they’re working optimally — rather than losing business due to uncomfortable environments during this important time.
Technology like IoT keeps them on top of their equipment data — even escalating issues through email alerts — to make more informed decisions and preempt problems. With a new level of empowerment, they can champion changes that help advance their organizations and achieve sustainability goals.
— Jason Roeder is senior director of product management at Powerhouse Dynamics, a Newton, Massachusetts-based provider of Internet of Things (IoT) solutions for multi-unit restaurants, retailers and other commercial organizations. Visit www.powerhousedynamics.com.